Antifreeze Cable Gel: What It Is and What You Need to Know
Antifreeze cable gel is used to protect fiber optic cables from the crushing forces of ice in a conduit. It is not intended for use with electrical cables and should only be used in fiber optic conduit systems.
Ice Kills Fiber Optic Signals
It is common for fiber optic conduit systems to contain water. This can happen when conduit couplings are not sealed properly, and ground water seeps into the conduit system over time. Another common source of water in conduits, which is more difficult to prevent, is condensation created by temperature differentials in the duct system itself. Temperature differences are common at transitions from the insulated underground environment to above-ground structures where freezing temperatures penetrate the conduit.
When water from infiltration or condensation is present in a conduit system below the frost line, it is generally not problematic. However, when conduit sections holding water are located above the frost line, such as in bridge crossings, culverts, or shallow ducts, the water expands as it freezes to bend or crush the glass fiber strands that carry the signal in a fiber optic cable. The result of this ice formation in the conduit is signal attenuation (degradation of speed or quality of the signal) or permanent damage to the fiber optic cable preventing any data transmission at all. These intermittent or permanent failures can represent enormous costs in downtime to the network owner and disruption of critical services.
A common practice that has been used to counteract damage to cables from ice formation is the use of weep holes, which are teardrop-shaped drainage holes drilled into exposed conduit. However, this practice does not prevent water accumulation, and weep holes often get plugged by debris and insects. Since fiber optic cable networks are intended to be closed systems, the use of weep holes is counterintuitive.
Related Content: How to Avoid Crushing Fiber Cable During Installation |
A more reliable and cost-effective solution is available to safely protect and prevent fiber optic cables from ice damage. This is the use of an encapsulating antifreeze cable gel. It can be effectively installed into the conduit along with a new cable installation or retroactively placed during repair and inspection work. Even though the use of antifreeze cable gel has been around for 30 years, there are many out there today who are unaware of its existence.
What is Encapsulating Antifreeze Cable Gel, and What Key Properties Should I Seek?
Antifreeze cable gel is a concentrated, water-soluble, viscous gel that has been tested for long-term compatibility with all common fiber optic cable jacket materials and conduit types. It is pumped into the space between the fiber optic cable and the innerduct to force water out and form a protective barrier that will not crystalize in sub-freezing temperatures. The temperature use range for antifreeze cable gel is -50°F – 120°F (-45°C to 50°C) . It is held in place by conduit sealants on either end of the installation that allow re-entry to the conduit system for future need. For installations where the conduit is not easily accessible for sealant placement, a special chemical duct block was developed that can be installed through the same application device that delivers the antifreeze gel. Read the Technical Brief for further information on the key properties of an effective antifreeze gel.
How Antifreeze Cable Gel Works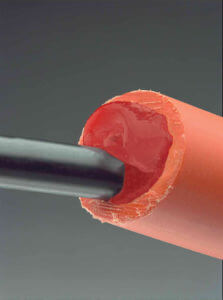
Antifreeze gel is a cable-compatible compound that will withstand freezing down to temperatures as low as -50°F (-45°C). It is injected into a conduit system to occupy voids that can be filled by water infiltration over time. It is installed using a high-ratio grease pump and high-pressure insertion hose. First, the hose is inserted into the innerduct to a predetermined sealed point in the conduit system. The pump is then activated, and the hose slowly drawn back towards the mouth of the duct as the gel is deployed. The antifreeze gel completely fills the innerduct encapsulating and insulating the cable(s). During the injection process, the antifreeze gel displaces existing water, which is pushed back to escape the mouth of the duct where the insertion hose enters it. (If ice has already formed inside the conduit system, it must be thawed before application of antifreeze gel.) Once injection is complete, a robust duct sealant is placed at the conduit entrance to keep the gel in place over the long term.
How Long Should Antifreeze Cable Gel Last?
Antifreeze cable gel is sufficiently concentrated to absorb some environmental water ingress over time and maintain its protective functionality. Properly installed antifreeze gel applications are expected to survive the lifespan of the cable, or multiple decades. To ensure the longest performance, ensure conduit couplings are intact and conduit openings are sealed with an appropriate conduit sealant.
Related Product: Polywater IceFree Encapsulating Antifreeze Gel System |
Origin of Antifreeze Cable Gel
Antifreeze cable gel was developed by Polywater in the early 1990’s when North America was transitioning from copper cables to fiber optics to support the digital revolution. At that time, new fiber optic network owners were noticing service interruptions during winter months but did not yet understand why it was occurring, so studies were performed to uncover the cause. Since Polywater had an established knowledge of materials science with cable components, they were consulted to help solve the problem of ice formation in susceptible conduits. Today, the formulation Polywater introduced more than 30 years ago, Polywater® IceFree™, is still the only encapsulating antifreeze cable gel solution available. Time has proven that it is a unique and effective solution to prevent ice damage to fiber optics and keep networks running at optimal performance levels.