How Prelubrication Increases the Odds of a Successful Cable Pull
In the surprisingly complex science of cable pulling lubrication there is an often overlooked concept, one that can help maximize friction reduction, optimize pull length, reduce damage and delay, and increase installation success. It hinges on one of the immutable laws of lubrication; that no matter how good the lubricant, friction reduction will not occur if the lubricant is not present where most needed — typically those troublesome bends far down the conduit. This is why the broader topic of lubricant application is so fundamentally important. But lubricant application need not be limited to pouring or slathering lube on the cable during the pull. Application can include prelubrication of the conduit prior to pulling. This is a particularly effective strategy on long, difficult pulls where the cost of cable damage or pull failure is high.
Prelubrication methodology depends on the conduit size and type but can include mandrels and other types of spreader devices, Front End Pack™ bags, or air pressure (blowing the lubricant into a conduit). This first in a series of articles discusses the advantages of the various methods and their suitability to particular pulling situations.
Related Content:The Science of Cable Lubrication: Film Thickness and Quantity Recommendations |
Front End Packs
The Front End Pack (FEP) is a conduit-sized bag of cable pulling lubricant. This specialized system was developed specifically for lubrication during cable pulling. The bag is attached to the winch line and sliced open as it enters the conduit. It deposits lubricant in front of the cable being pulled. This simple design reduces labor and mess. The real benefit is that it prelubricates the conduit and results in better lubrication. Front End Packs lubricate far into the conduit where lubrication may be inadequate.
Front End Packs are available in two sizes for use:
Small for 2-inch to 3-inch (50 to 75 mm) conduits
Medium for 3½-inch to 5-inch (90 to 125 mm) conduits
While the use of FEPs is a convenient method for prelubricating conduit, prelubricating the conduit with a spreader can also produce excellent results.
Prelubrication Using Mandrel or Spreader
For more difficult pulls and for larger conduit sizes, prelubrication using a spreader device is recommended. There are a few devices already on the market for cleaning and proving the conduit. These spreaders were tested for effectiveness and practicality.
Photo 1: Disk lube spreader. This is primarily used to clean the duct. The composite rings are tapered. The material will flex but not compress. The fit is not tight.
Related Content: FAQ – Cable Pulling, Lubrication, and Tension |
Photo 2: Flexible mandrel. This is primarily used to clean the duct. The polyurethane disks are tapered with a convex contact that allows the mandrel to move through tight bends. The fit is not tight.
Photo 3: Inflatable Rubber plug. This is primarily used to clean the duct. The plug is inflated, but the fit is still not tight.
During testing, the recommended quantity of lubricant was added to the conduit and “spread” with the disk spreader, flexible mandrel, and inflatable rubber plug. The lubricant pooled early in the length of conduit (see Photo 4), and there was not enough lubricant to coat the entire test run.
Photo 4: Excess lubricant at the bottom of the conduit. The disk spreader leaves a streaked, heavy coat of lubricant at the bottom of the duct.
The disk spreader, flexible mandrel, and inflatable rubber plug do not spread the lubricant evenly. When tested, each of these methods left heavy streaks of lubricant mostly at the bottom of the conduit. The lubricant did not coat evenly, nor did it coat the top parts of the conduit. Because these devices left pools of lubricant during the initial part of the duct, the lubrication was incomplete in the last sections of the conduit.
Foam Disk Spreaders
It has been shown that one of the best ways to spread lubricant is the use of a compressed foam disk or multiple disks. For this testing, a marine-grade upholstery foam was used to cut disks to the Outer Diameter (OD) size of the conduit.
Photo 5: Compressed foam. The foam is cut slightly larger, even with the outside diameter of the conduit. It is compressed to fit completely within the space.
Photo 6: Another version of the foam spreader uses 2 large foam disks (seen hanging). Different versions of the foam spreader have been used in large cable installations.
Photo 7: Compressed foam leaves an even coating of lubricant.
In this test, a thin layer of lubricant was coated throughout the entire surface of the conduit. As shown in Photo 7, this coating shows no signs of pooling and only limited amounts of lubricant streaking. During this test, the lubricant spread evenly through the full length of the conduit.
Related Content: Planning Cabling Projects Improves Success and Safety |
Lubricant Quantity and Coating Thickness
The lubricant coat left by a tight-fitting sponge is somewhere between 2 to 5 mils (0.05 to 0.125 mm). In addition, a small amount of excess lubricant is required to fill and flow through the top of the conduit for this lubricant spreading process.
Photo 8: Lubricant is added in front of sponge for spreading.
As lubricant is spread through the conduit, it leaves a thin layer. As the sponge is pulled through the conduit, the lubricant charge is slowly depleted as it coats both the top and bottom of the duct.
The amount of lubricant required for prelubrication is approximately half the standard lubricant recommended quantity, along with some excess to fill the space in front of the sponge spreader as shown in Photo 8. Excess lubricant is needed so that it fills the conduit ahead of the spreader, especially near the end of the pull length.
Prelubrication Lubricant Quantity Formula:
Q = quantity needed in gallons (liters)
L = length of the pull in feet (meters)
D = ID (Inner Diameter) of the conduit in inches (mm)
k = 0.0008 (0.0004 if metric units) – half the standard lubricant quantity
c = .004 (1 x 10-6 if metric units)
Chart 1: Recommended Prelubricant Quantity in Gallons/Liters
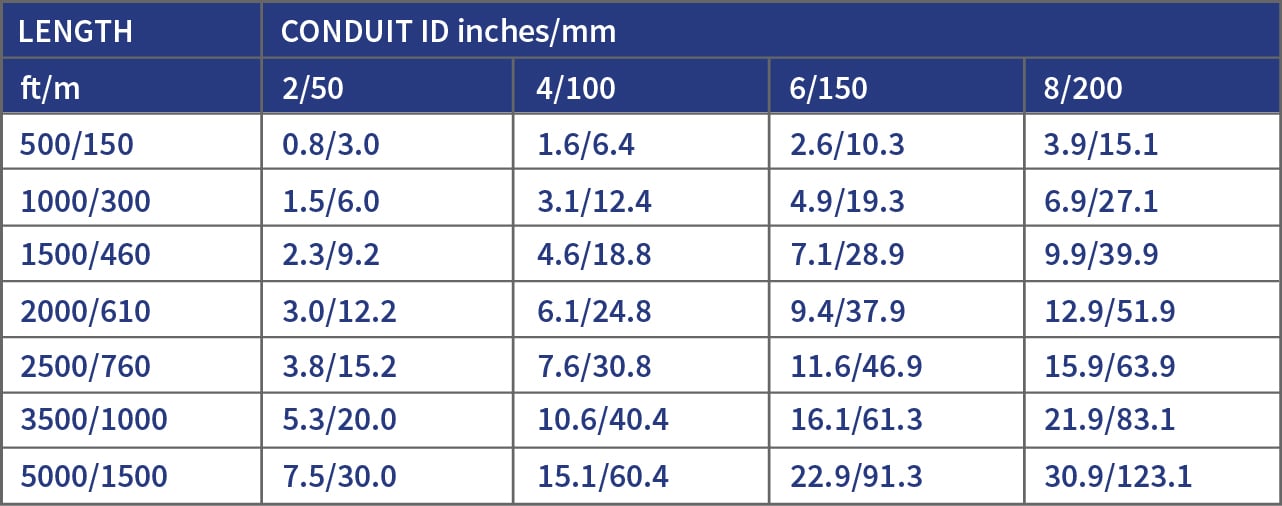
How Long Does Prelubrication Last?
Lubrication via FEP is typically done contemporaneously with cable pulling but is still considered prelubrication because the bags are attached to the winch or pulling rope and precede the cable down the conduit run. The efficacy of FEP prelubrication is thus not in doubt. However, prelubrication via spreader is often done as a separate step, and it may be days or even weeks before the cable is pulled. Depending on lubricant choice, prelubrication several weeks in advance is still a good option. As shown in Graph 2, several lubricants work well even after they are fully dried.
Graph 1: Coefficient of Friction After Drying
These lubricants remain effective even after drying. The coefficient of friction (COF) remains low after drying for one week at accelerated temperatures. Prelubricating the conduit – even several weeks ahead – is an effective practice to produce low COFs and keep cable tensions low.
Related Content: Underground Cable-in-Duct Installation: 5 Trends to Consider |
Achieve higher installation success with prelubrication
In our many decades of field experience we’ve seen conduit prelubrication used in only a small percentage pulling situations. Though underutilized, it remains a highly effective method of friction reduction in critically important cable pulls. It can help guarantee adequate lubricant is present where needed most in the conduit. This increases the odds of a successful pull and lowers overall project costs by eliminating cable and equipment damage and unnecessary delays. Installers tasked with difficult pulls should assess the conduit and cable type parameters and select an appropriate prelubrication method. When prelubrication is performed in conjunction with application of lubricant during the pull, the lowest pulling tensions and highest installation success rates can be achieved.